Trippe Hall
Penn State University
Erie, PA
Kayla Clatty
Construction Management
Advisor: Dr. David Riley
General Building Information
Building Name
Occupancy
Trippe Hall
Dormitory
Residential Type R-2
Business Area on 1st Floor Type B
Multi-Purpose Rooms Type A-3
60,000 SF
251
4 (above ground)
Size
Beds
Floors
Project Team
Owner
General Contractor
Architect of Record
Design Architect
MEP Engineer
Structural Engineer
Civil Engineer
Landscape Architect
Building Overview
Penn State is expanding their satellite campus in Erie in order to respond to the increasing demand of student applications. Since there are so many students on the wait-list to join Penn State Behrend, adding a new dormitory would provide living quarters for 251 more students on campus. A new dormitory is being built on the Southeast side of the campus.
The construction of the building is a 4-story dormitory that embraces the culture of the campus. It has a brick facade and metal sloped roof that resembles other dormitory buildings. Also, all buildings on campus are named after commanders or ships that fought in the Battle of Lake Erie. Trippe was a ship in the United States Navy. With the open common areas and smaller living areas, this new dormitory will encourage students to spend time in more social situations that could enable their confidence and soft skills.
Major National Model Codes
IBC 2009
International Energy Conservation Code 2009
International Fire Code 2009
International Fuel Gas Code 2009
International Mechanical Code 2009
International Performance Code for Building and Facilities 2009
International Plumbing Code 2009
ADA 2010
Zoning
Min. Front Yard Depth: 50 ft (from Jordan rd.)
0 ft (from college owned rd.)
Min. Side Yard Depth: 20 ft (between buildings)
100 ft (from residential use)
Min. Rear Yard Depth: 20 ft (between buildings)
100 ft (from residential use)
Max. Height of Structure: 45 ft
Max. Building Coverage: 30%
BUILDING ENCLOSURE
Facade
Brick
Composed of nominal clay face brick. The brick used on this project was designed to match the brick from another dormitory on campus, Senat Hall. The brick on the exterior walls are not a structural component of the building.
Glazing
Storefront and curtain wall is composed of aluminum alloy framing and reinforced to support imposed loads. Glazing consists of many types of float glass and insulating-glass in order to adhere to the building envelope, light transmissions, and tempering. Also, spandrel glass is used in areas where privacy is necessary.
Stone
Natural limestone with a gray, light gray, and white color range composed of different rectangular sizes are used to break up the repetitive feel of a brick facade.
Metal Wall Panels
The metal wall panels are composed of coil-coated aluminum sheet facing with insulation.

Sustainability
Natural ventilation is utilized in the rooms with operable windows. Solar shades are provided for all operable windows and curtain walls in study lounges and conference rooms, so that day lighting can be controlled. At least 80% of the building materials are from the local region. This also helps with becoming LEED certified. The project’s pre-certification estimate shows that it will be LEED certified, and likely to gain a silver or gold rating.
In order to control runoff, a retention pond is located on the site to collect water and prevent it from contaminating adjacent land. This is a cost-effective way to control the effects of weather once the project is complete since Erie is known for harsh winters and a large amount of rain.
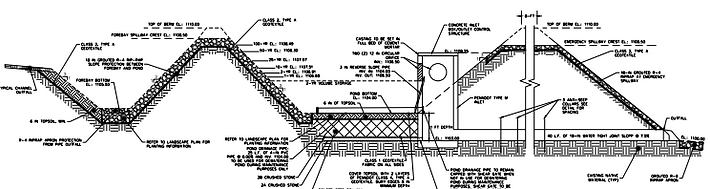

Roof System
TPO (Thermoplastic Polyolefin)
The fabric-reinforced TPO shall be white or off-white as selected by the architect and use board insulation. In order to have a usable surface for the AHUs on the project, the TPO roof is provided only in areas where a flat roof is needed.
Metal Roof
Metal roof panels are formed with vertical ribs at panel edges and a flat pan between ribs where edges of the pans are fastened together. The metal roof panels are attached to self-adhering, high temperature underlayment and asphalt adhesive for thermal and moisture protection.
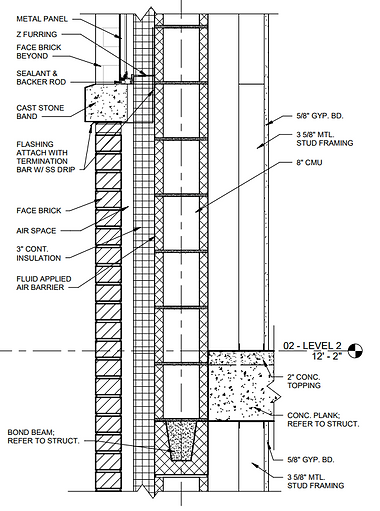
Construction
Penn State Erie, The Behrend College is expanding the campus by providing a new dormitory that will hold 251 additional beds.This will increase enrollment at the campus and provide more on-campus housing for students that live out of town.The university is located near Interstate 90 in Erie, PA.Jordan Road splits the campus, and a lot of foot traffic occurs on this road.For this, construction has been rerouted to use Technology Drive in order to maintain safety for the students.The site is located in the southern part of campus, away from most of the dining areas and buildings with classes.Trippe Hall is a Design-Build project that hired the general contractor, Turner Construction, as the design-builder.The general contractor hired another firm, Noelker and Hull Associates, Inc., to partake in the design-build project. The schedule for the construction of the project will start in December 2016 and be completed in July 2018. Along with this, project documents were not 100% complete once construction started, but that was intended when the delivery method was decided to be Design-Build.
Structural
Construction of the structural system includes multiple structural components within the system. Concrete spread footings (3000 psi), continuous strip footings (3000 psi), and piers (5000 psi) are used as the foundation of the building. The slab on grade for the first level of the building is 4000 psi with a wire mesh added to prevent cracking. Where the spread footings and continuous strip footings are located, concrete masonry units (CMUs) are placed on top to provide load bearing walls with fully grouted and reinforced areas where specified within the wall. The reinforcing used in the walls are #6 and #8 sizes. Each wall that requires reinforcing and grout has a detail showing the specific requirements for the amount of rebar types required for that area. In areas where the floor spans are large or the exterior façade is a curtain wall, hollow structural steel (HSS) and steel wide flanges are used to provide open floor plans where the masonry walls are not beneficial to use. The steel columns and beams have a large range of sizes depending on the span of the member. The HSS ranges from 6x6x3/8 to 10x10x1/2. The steel wide flanges range from W8x24 to W24x76. For the floor system, precast concrete planks are placed on the masonry walls and steel beams. The masonry walls are cut to insert the planks, and they also require steel angles to support the wall where the plank rests. On top of the precast planks, a concrete topping slab (4000 psi) is placed for uniformity. The process of placing CMU block, steel, and precast planks will occur on each floor up to the 4th floor. Once the structure is complete, trusses are placed on the 4th floor masonry walls to provide support for the roof system. There are seven types of truss designs with varying web configurations used for the roof in order to provide the proper support and slope for the roof. These trusses are prefabricated cold-formed steel.
Mechanical
The mechanical system of the building is simpler than other buildings that require complex code requirements. Fan coil units (FCU) are located in each of the dormitory rooms to provide the ability to change thermostats in each room according to the user’s comfort levels. The FCUs provide between 180 – 850 cfm of supply air depending on the size of the space. Hot and cold water piping are run to each FCU for the finned-tube heat exchangers within the units. Three split system air conditioner units are provided for the conditioning of the public spaces. Along with this, there is outside air that is supplied by AHU-1 (air handling unit) and AHU-2 to all spaces in the building in order to maintain a healthy airflow throughout the building. AHU-1 produces 4500 cfm outside air and AHU-2 produces 4000 cfm outside air. Variable frequency drivers (VFD) are located at each exhaust fan and supply fan for both AHUs to provide better control of the air flow of the spaces. In order to have an efficient AHU, heat recovery wheels are located in each unit to harness some of the air that was already conditioned for the spaces to be filtered and reused. Along with this, two highly efficient gas boilers are used to heat the water supplied to the FCUs in the building. Radiant heat panels are located in all bathrooms that are located near the exterior wall of the building to provide support for accurate conditioning of the space.
Electrical
The new duct bank will tie into the existing duct bank between the adjacent dormitory buildings, and then the new duct bank will tie into the northeast and northwest portions of the building. In the dormitory rooms, double-duplex receptacles are located near each desk and duplex receptacles are located by the dressers and beds. For safety, ground fault circuits are located in all of the single-use restrooms. The offices have one duplex receptacle and two double-duplex receptacles on either side of the wall to provide flexibility within the space. The switchgear is a 480Y/277V, 1200A 3-phase equipment that provides power for the entire building. A backup generator provides 480Y/277V 3-phase power to the building in case of an outage. Wireless data access will be provided in each of the dormitory rooms, which is different from the older dormitories on campus.
Lighting
All LED fixtures were used to make the system more efficient. The majority of lights have a universal voltage requirement, the exterior lighting requires 120 V, and the stairwell and exit signs require 277 V. Dormitories have a 4” downlight located near the entranceway with a 4’long up light above each student’s desk. The lights switches in the dormitory rooms have dimming ability, so that the occupant can have control of the intensity of the light system. The hallways are equipped with 4” semi-diffuse downlight fixtures and 6’ long lights with a frosted lens for aesthetics. The single-person use restrooms have a 4” downlight in the center and above the shower, while the vanity has a 3’ long light with a frosted lens to subdue a harsh light near the mirror. Since the large common area/meeting room is supposed to provide an open feeling in the space, suspended 4’ and 8’ long pendant lights with frosted lenses contribute to a more relaxed feeling inside the double-high ceiling space. Office space conference areas are equipped with recessed light fixtures that are 2’x2’ and an acrylic lens. The back of house and maintenance rooms have standard lighting with a steel housing for protection from getting damaged. Dormitory rooms, offices, bathrooms, meeting areas, conference areas, and back of house areas have vacancy sensors to save energy when occupants are not located in those areas.
Fire Protection
The sprinkler system uses a wet pipe system; however, dry sprinkler heads will be located in the bicycle storage area on the first level. One standpipe is located in either section of the building. Underground piping is required to follow NFPA 13 or 24 standards, and all pipe should be wrapped with a bituminous coating. Above ground piping will be welded or seamless steel according to NFPA 13, and threaded piping should have a minimum of schedule 40 wall thickness or schedule 10 wall thickness for roll grooved/welded piping. Joint firestopping systems are used for any penetration through a fire-rated was is required. Joints that are between fire-rated walls will comply with ASTM E 1966 or UL 2079, joints at exterior curtain walls or floor intersections will comply with ASTM E 2307, and joints in smoke barriers will comply with UL 2079 and not exceed 5 cfm/ft. at ambient and elevated temperatures, and exposed joints will comply with ASTM E 84 index for flame spread and smoke development. Certain areas in the building will follow NFPA 13 standards for Occupancy Hazard Classification if the areas are marked OH-1 or OH-2 (occupancy hazard).